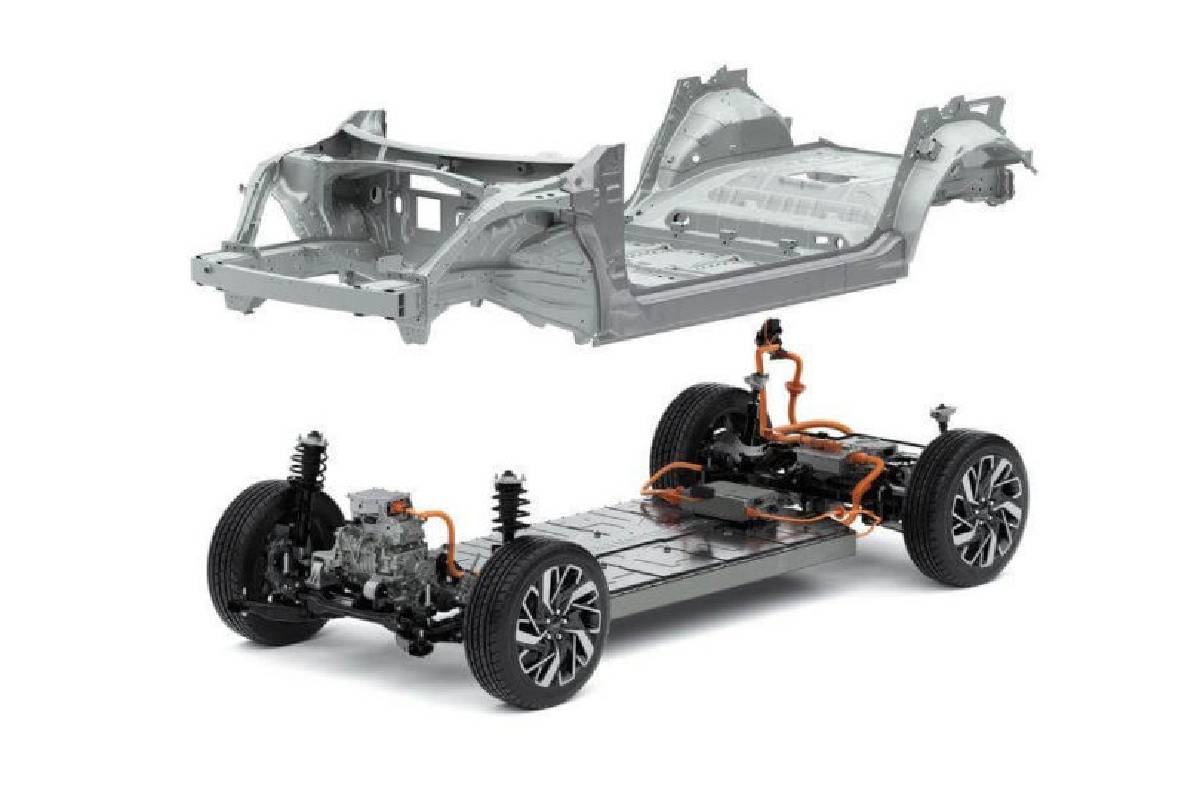
EV platforms are a base upon which a vehicle is built. We determine the rigidity of the vehicle, the cabin’s layout, and the appropriate engineering decisions, including the motor and transmission, by its design and requirements.
Up until recently, traditional automakers produced ICE automobiles were in a dilemma. Should they alter their current EV platforms to make room for an electric drivetrain instead of scrapping all of their old ones and building new ones specifically for EVs?
Regarding this, there is no industry-wide agreement. Some manufacturers alter current ICE EV platforms, some design whole new EV platforms, while others take a hybrid approach by using both techniques on various vehicles.
Modified ICE Platforms
Typically, when building an ICE platform, manufacturers consider the future. Engineers must plan for it in their designs for it to support an all-electric car. Consider the VW group’s MQB platform as an illustration.
This platform was initially made to accommodate several propulsion technologies: all-electric vehicles, plug-in hybrids, natural gas, and gasoline and diesel. The advantage of this strategy is flexibility in product development and main use for the ICE automobiles.
BMW’s CLAR and FAAR platforms were both for ICE automobiles. It can also be used as the foundation for EVs. The “all in front” configuration is used by the vast majority of popular ICE vehicles.
This indicates the power delivery that occurs at the front axle. This happens if the engine and transmission are mounted transversely in the car. Therefore, this affects any electric vehicle built on the same ICE platform.
The longitudinal exhaust piping and potential 4WD hardware are typically predict the ICE platform, so when manufacturers replace those with batteries, they must create them in intricate designs like “H” or “T.” It is challenging to have them with the highest capacities because of their complexity. Additionally, it restricts versatility, making it rare for different capacities to be on the same model.
In addition, a tunnel below the back passenger area divides it in half. This design has some drawbacks, including poor space use and troublesome torque handling. On platforms like BMW’s CLAR that are for rear-wheel drive conversion, the torque handling penalty is less noticeable.
Dedicated EV platforms
Due to its lengthy development and high R&D expenses, this platform raises car costs and delays market launch. They are ultimately a superior option, though, because of their many advantages. If you’ve ever driven a fast car, you’ve undoubtedly noticed how the seat scrapes on your back while the car speeds.
This indicates that the car’s weight shifts to the back while also slightly elevating the front and squatting the rear. Sending the large amount of torque that an electric motor produces nearly instantaneously to the back axle will allow you to fully utilize it without losing traction.
Because of this, when an automobile has only one electric motor, the back axle is often powered. Because there are no front driveshafts, the car will have a better turning cycle.
Another benefit of the EV platform is its simpler battery design, which is rectangular between the vehicle’s axles and enables the offering of various energy contents by increasing the number of module slots in the battery pack.
However, the “skateboard” structure of the rear suspension design is complex. Only transverse links are feasible in this situation, eliminating the usage of a multi-link fully independent suspension with longitudinal links (particularly in tiny automobiles).